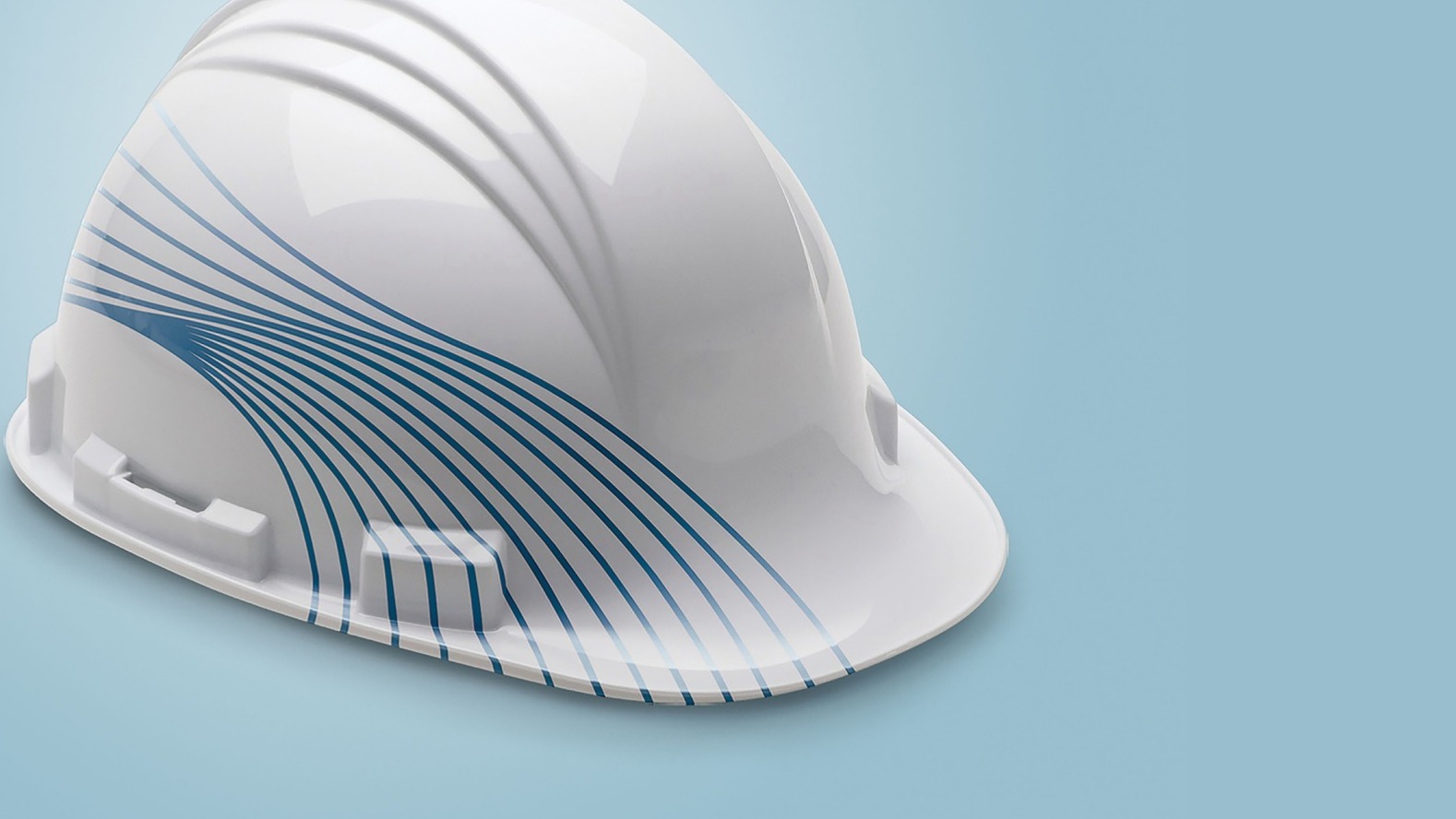
Insulation Cost per Square Foot in Shreveport
Insulation Cost per Square Foot in Shreveport, LA
Insulating your home is an important investment that can significantly improve energy efficiency, reduce utility costs, and enhance overall comfort. When considering insulation, one crucial aspect to evaluate is the cost. Understanding the insulation cost per square foot in Shreveport will help you make informed decisions about the materials, installation, and budgeting.
Insulation plays a vital role in maintaining a comfortable indoor environment while minimizing energy consumption. By creating a barrier against heat transfer, insulation helps keep your home cool in the summer and warm in the winter.
Additionally, it reduces noise transmission and contributes to a more sustainable living space. However, the cost of insulation varies depending on several factors, and it is important to understand these variables before making a decision.
In this article, we will explore the factors that affect insulation cost, common types of insulation materials, average costs per square foot in Shreveport, and other essential considerations.
Importance of Insulation
Insulation is an essential component of any home or building as it provides thermal resistance, which prevents heat from escaping or entering the premises. By reducing heat transfer, insulation helps maintain a consistent indoor temperature, reducing the need for excessive heating or cooling.
This, in turn, leads to lower energy bills and a reduced carbon footprint. Insulation also helps control condensation, which can contribute to mold growth and structural damage. Overall, a well-insulated space offers numerous benefits for both comfort and energy efficiency.
Factors Affecting Insulation Cost
Several factors influence the cost of insulation installation. Understanding these factors will help you estimate the overall expense and choose the most suitable insulation type for your needs. The following are some key considerations:
1. Type of Insulation Material
Different insulation materials come with varying costs. The type of insulation you choose will depend on factors such as effectiveness, durability, and budget. Some commonly used insulation materials include:
Fiberglass Insulation
Fiberglass insulation is one of the most popular and cost-effective options. It is composed of fine glass fibers and is available as loose-fill or batts. Fiberglass insulation is known for its excellent thermal performance and ease of installation. On average, it can cost between $0.70 to $1.20 per square foot for materials.
Spray Foam Insulation
Spray foam insulation is a versatile option that expands upon application, providing a seamless barrier against air infiltration. While it tends to be more expensive than other options, its superior insulating properties and air sealing capabilities can lead to long-term energy savings. The cost of spray foam insulation typically ranges from $1.50 to $3.00 per square foot for materials.
Cellulose Insulation
Cellulose insulation is made from recycled paper and treated with fire-retardant chemicals. It is an eco-friendly option that offers good thermal performance and sound absorption qualities. Cellulose insulation is commonly blown in cavities in walls or attics. The average can cost around $1.00 to $1.50 per square foot for materials.
Reflective Insulation
Reflective insulation consists of foil-faced materials that reflect radiant heat. It is commonly used in hot climates to reduce heat gain. Reflective insulation is relatively inexpensive and easy to install.
Rockwool Insulation
Rockwool insulation, also known as mineral wool insulation, provides excellent fire resistance and soundproofing properties. It generally costs between $1.50 to $2.50 per square foot for materials.
Polyurethane Foam Board Insulation
Polyurethane foam board insulation, often used in exterior applications, can cost around $1.50 to $3.00 per square foot for materials.
2. Area to be Insulated
The size of the area to be insulated directly impacts the overall cost. Larger projects will need more materials and manpower, resulting in higher costs. It's essential to measure and calculate the square footage accurately to obtain an accurate estimate.
3. Complexity of Installation
The complexity of the installation process can influence the cost. Insulating irregular spaces, inaccessible areas, or structures with unique architectural features may require additional time and effort, resulting in higher labor costs.
Skill and Expertise: Complex insulation installations often require a higher level of skill and expertise. Certain insulation materials or techniques may necessitate specialized training or certification. Insulation contractors with advanced skills and experience in handling intricate installations are likely to charge higher labor rates to account for their expertise.
Preparation and Planning: Complex insulation installations typically require detailed preparation and planning. This includes assessing the specific needs of the space, taking accurate measurements, and determining the best approach to ensure optimal insulation performance. The time and effort involved in this preparation phase contribute to increased labor costs.
Customization and Accessibility: In complex insulation projects, customization and addressing unique requirements are often necessary. This might involve intricate cuts, fitting insulation around obstacles or irregular surfaces, or insulating hard-to-reach areas. These additional steps require extra time and effort, resulting in increased labor costs.
Specialized Equipment and Tools: Complex insulation installations may require the use of specialized equipment or tools. For example, installing insulation in tight spaces or at elevated heights may require scaffolding, lifts, or other specialized equipment for safe and efficient installation. The cost of renting or operating such equipment is factored into the labor cost.
Time and Labor Intensity: Complex installations generally require more time and labor to complete. Installers may need to spend additional hours ensuring proper insulation placement, sealing air gaps, or integrating insulation with other building components. The increased time commitment translates to higher labor costs.
Code Compliance and Regulations: In some cases, complex insulation installations must meet specific building codes or regulations. This may involve additional steps, such as fireproofing, soundproofing, or meeting energy efficiency requirements. Ensuring compliance with these regulations adds complexity to the installation process, resulting in higher labor costs.
4. Labor Costs
Labor costs play a significant role in determining the overall insulation cost. Hiring experienced professionals ensures proper installation and can contribute to the longevity and effectiveness of the insulation. Labor costs may vary depending on the region and the expertise of the contractors.
5. Additional Accessories
In some cases, additional accessories such as vapor barriers or soundproofing materials may be necessary. These accessories can add to the overall insulation cost. It's important to consult with professionals to determine the need for any supplementary products.
Conclusion
It's important to note that these figures are approximate and can vary depending on factors such as the insulation thickness, brand, quality, and location. Additionally, the costs mentioned are for materials only and do not include labor or installation fees. Hiring a professional insulation contractor will incur additional costs for their services.
To get a more accurate estimate for your specific project, it's recommended to consult with insulation suppliers or contractors in your area. They can provide detailed quotes based on your insulation needs, the size of the area to be insulated, and any other specific requirements you may have.